국내 기술로 상용화가 가능한 차량용 에어덕트가 개발됐다. 국산 에어덕트 개발은 수입품(프랑스산 에어덕트) 의존도를 줄여 국내 자동차 업계의 자립도를 높이는 역할을 할 것으로 기대된다.
한국기계연구원(이하 기계연)은 배승훈 부산기계기술연구센터 연구팀·유진 에스엠알시㈜(유진 SMRC A.T)·에스에이치코리아 등으로 구성된 공동연구팀이 자동차 콕핏 모듈(Cockpit Module)의 에어덕트 제조기술을 획기적으로 개선, 완성차 규격을 만족한 에어덕트를 개발하는 데 성공했다고 2일 밝혔다.
콕핏 모듈은 자동차 운전석을 구성하는 핵심 부품의 통합된 기본 단위와 계기판, 공조장치, 라디오, 시계, 소형품 수납장치 등을 아우른다. 운전자의 기능조작과 정보 확인을 돕는 역할을 한다.
기존 에어덕트는 고밀도 폴리에틸렌(HDPE) 소재로 제작돼 무겁고 단열 성능이 부족했다. 또 열 손실이 크고, 조립 과정의 불편성과 소음 발생 등의 문제를 야기했다. 이 때문에 차량 연비를 떨어뜨리고, 사고 시 덕트가 깨져 운전자가 다칠 수 있는 안전상의 문제도 있었다.
공동연구팀이 개발한 에어덕트는 폼 시트를 활용해 기존 에어덕트 제품보다 무게를 60%가량 줄인 동시에 기밀성·소음 저감·안전성 등 부문에서 성능을 높인 것이 강점으로 꼽힌다.
무엇보다 이 에어덕트는 폼 시트를 적용한 진공 성형 및 핫나이프 공정으로 제작돼 기존 블로우 성형보다 불량률이 낮고, 복잡한 형상을 정밀하게 구현할 수 있어 생산성도 높일 수 있다.
진공 성형은 폼 시트를 예열한 후 금형에 넣고 진공상태에서 폼 시트를 금형의 형태로 성형하는 공정이다. 핫나이프 공정은 나이프 날을 예열한 후 에어덕트 형상에 맞게 컷팅할 수 있는 공정으로, 정밀한 절단이 가능한 장점을 가졌다.
공동연구팀은 개발한 에어덕트의 신뢰성 확보를 위해 성능평가를 수행, 완성차 규격을 충족하는 것도 확인했다. 이 과정에서 PE 혹은 폴리프로필렌(PP) 등 고분자 구조물의 동적 물성을 추출하는 기술도 확보했다.
배 선임연구원은 “공동연구팀이 개발한 에어덕트는 기존 프랑스산 에어덕트의 단점을 보완, 국산화와 상용화를 가능하게 할 것으로 기대된다”며 “향후 완성차 업계가 다양한 차종에 적용할 수 있을 것으로 보인다”고 말했다.
한편 이번 연구는 산업통상자원부와 한국산업기술기획평가원의 ‘자동차산업 기술개발(그린카)’ 과제 지원을 받아 수행됐다.
대전=정일웅 기자 jiw3061@asiae.co.kr
꼭 봐야할 주요뉴스
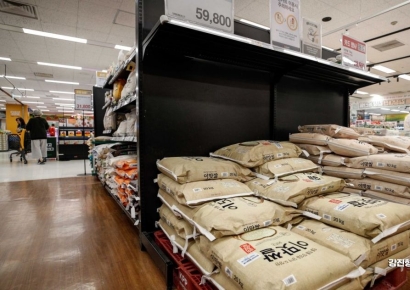
<ⓒ투자가를 위한 경제콘텐츠 플랫폼, 아시아경제(www.asiae.co.kr) 무단전재 배포금지>